Ever had someone ask you, “Do you have black powder?” Anyone who has done any powder coating knows that there’s a lot of colors qualifying as “black.” Doing two colors of powder coating is similar in a way; there’s more than one way to do it right – and being armed with some knowledge can help you get it right more often than not. What is important to recognize is that it takes a lot of extra time and care – so charge accordingly!
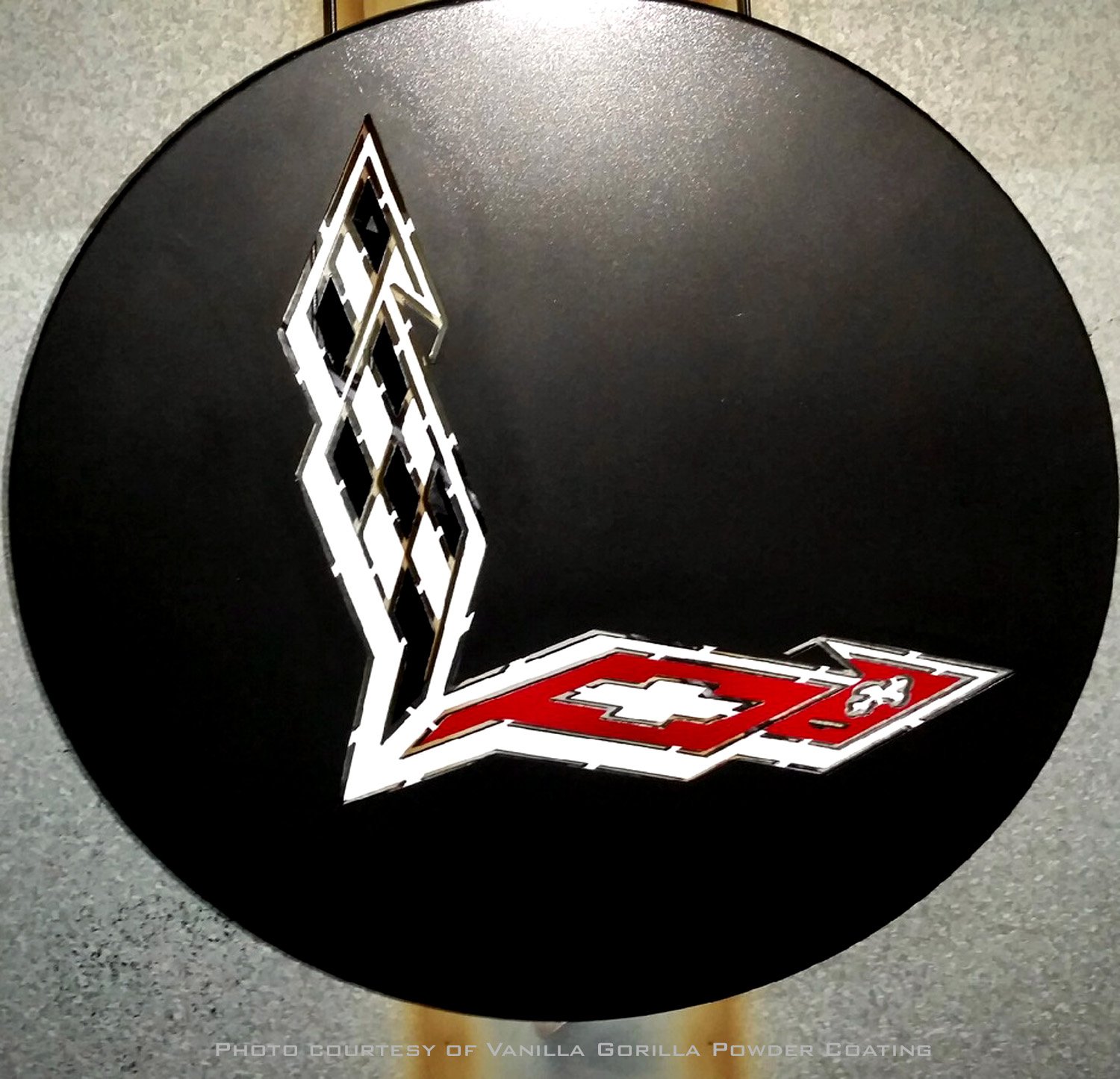
Multiple-Color Powder Coating, Corvette Table Top
There are many variables that come into play when doing two-color powder coating: Powder type, heat requirements, size/mass of part, flow-out temperature for each powder, appropriate tape to use, and more.
Here are two different procedures some powder coaters follow when putting two colors of powder on one part is as follows:
Procedure #1
- Clean part thoroughly
- Shoot part with first color
- Partially cure* first color in oven (do not full cure, especially white powder)
- Let part cool completely
- Mask areas that are to remain first color
- Shoot part with second color, covering over unmasked first color areas
- Fully cure both powders in oven
- Remove part, let cool, remove tape (note: some tape removes more cleanly while part is still warm, especially if tape has gone through more than one oven cycle)
* - for high gloss first coat, cure to 75%. If matte/flat first coat, cure to 50%.
Viadon has all the high heat masking tapes you need to successfully powder coat multiple colors:
Procedure #2
- Clean and mask piece as per usual for a first coat
- Cure at minimum time and temperature for that powder manufacturer’s recommendations
- Remove from oven; allow part to completely cool
- Apply masking tape for second layer
- Apply powder, and partially cure – only enough to change the powder from a powder to just before “wetting out,” around 180-200 degrees F (see more info in paragraphs below about this)
- Remove part from oven, allow part to cool again
- Remove masking tape. Be careful of second coat in this condition!
- Place part back in oven, finish cure for recommended length of time
NOTE: Viadon strongly suggests practicing these procedures first on non-critical parts.
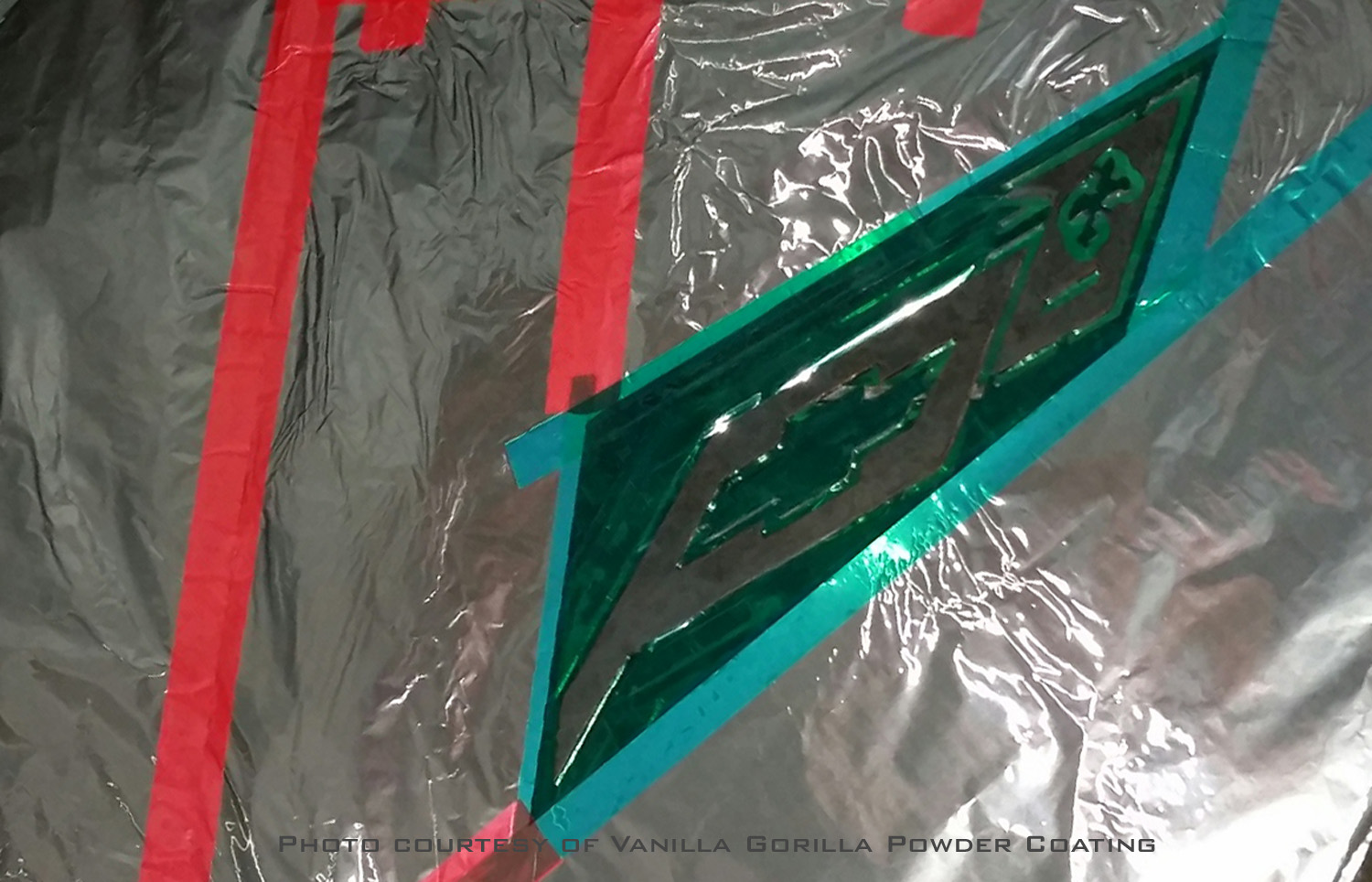
Initial Masking for Multiple-Color Powder Coating
These two options are all well and good for parts that are being fully covered, but what about when there are bare metal surfaces that must be kept bare after both colors? One could always use Procedure #2, and tape the same bare-metal area twice, but that can be very time-consuming. Short of that, the tape then must go through two heat cycles. This is where many powdercoaters run into problems. There are some solutions, but none that are hard-and-fast that work for every situation.
This is where practice and experimentation to perfect the technique are important, because just as there are tapes with differing qualities, there are powders with differing qualities too. Not every powder melts or flows at the same temperature, and lower mass parts will reach this temperature faster than more massive parts. These all need to be taken into consideration for two color powder coating.
“Intermittent Heat”
To start, keep in mind that all powder coating masking tapes are rated for “intermittent heat.” What this really means is that the adhesive, and sometimes the carrier (the plastic or fiber part of a tape), can only withstand a certain maximum temperature for a given period of time. For example, the popular green polyester powder coating tapes many American tape manufacturers produce (that Viadon carries) are rated to 400F for up to 1 hour. Longer than that, the tape can begin to shrink, and the adhesive can start to fail. Though many powders cure from 350°F to 380°F, that doesn’t lengthen that “intermittent heat” time frame by very long.
Remember that parts may take a good long while to fully heat up to allow a full cure. So the part may only be at 350F for 10 or 15 minutes, but it may have been in the oven for 45 minutes total time, in order to heat up the entire mass of metal to that temperature. This can cause tape failure when the part goes through a second cycle.
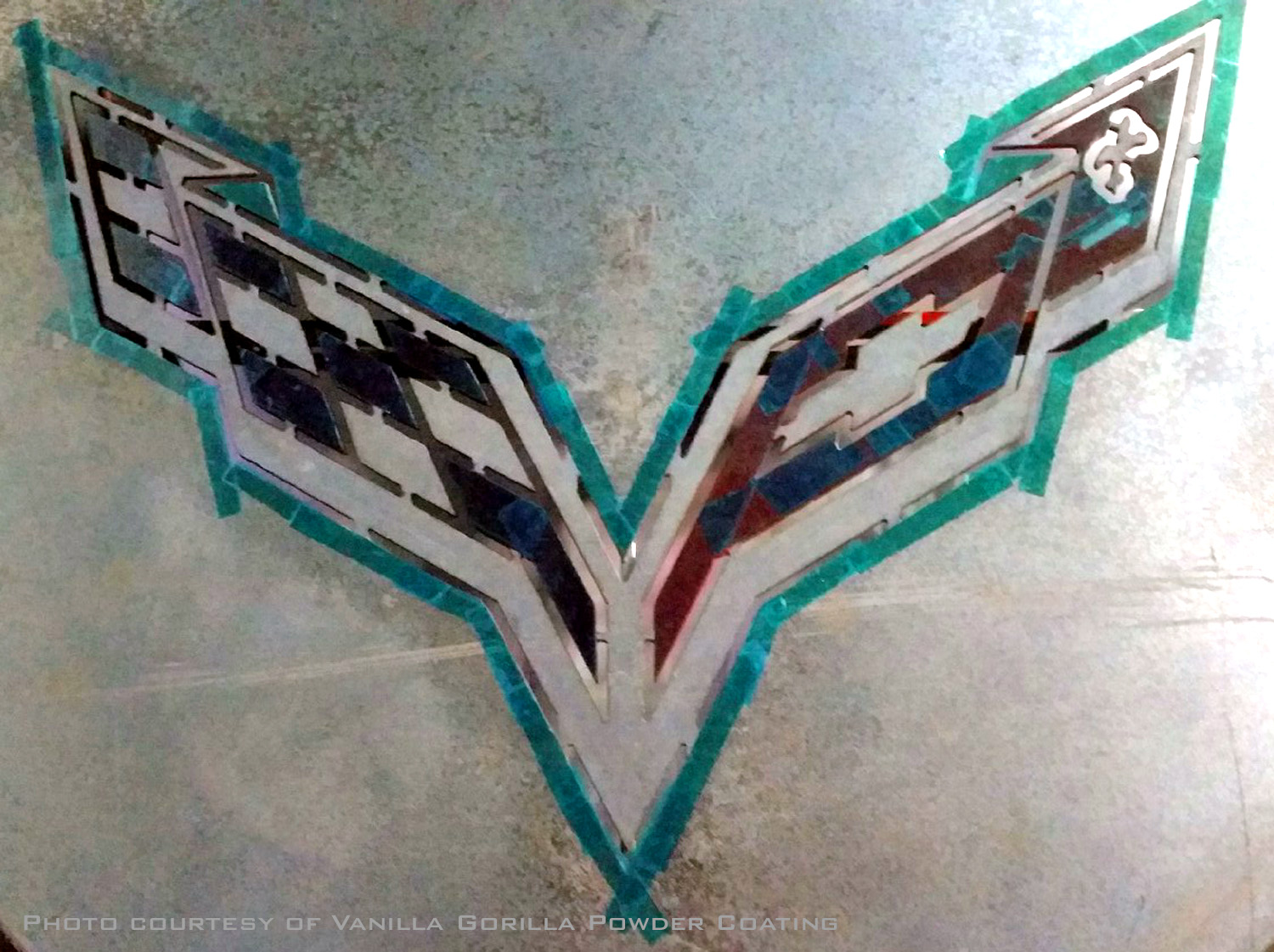
Partial Masking of Corvette-Insignia Table for Multiple-Color Powder Coating
For example, while the part itself may only be getting up to 180°F or 200°F, the tape is being subjected to that 400°F of the oven from the moment it goes inside. It may only take 20 minutes to get the part to 200°F, but even when you pull it out of the oven, the part is now radiating heat THROUGH the tape! And now you’re putting it back in for another full cure cycle.
The total time the tape is subjected to higher than ambient air temperatures may actually be well beyond 60 minutes total time.
What To Do
Try using a higher maximum temperature tape for the masked sections that must go through more than one oven cure cycle. Viadon’s orange polyester tape is rated to 425F; many customers have greater success with this tape for two color applications, because for smaller parts that heat upquickly, there is some additional temperature buffer between a 350F cure temp and the 425F max temp (18%), compared to the 400F tapes (12%). Many of our customers who tried two color powder coating and have only used the green polyester tape have achieved successful outcomes with our VOT orange polyester tape.
For larger parts or higher cure temperatures, a tape with even higher heat temperature ratings may be required. Both glass cloth and polyimide tapes offer 500F max temperatures. Glass cloth is thicker, at 7 mils, and may leave ridges if not removed prior to full cure oven cycles. Polyimide can leave cleaner lines, but due to its 1 mil thickness, may break when pulled off of fully cured parts, particularly for thicker powder applications.
When To Remove The Tape
So when IS the right time to remove tape when a part is warm? Many powdercoaters find that it varies – by powder, and by part. But a good rule of thumb is to heat the part to 180°F to 200°F. In many successful two color powder applications, the part is removed from the oven before the powder “flows out” or “wet” but after it has gone from powdery into a “melted” state. Our understanding is that there is a fine line before ‘wet’ and after ‘melted’ (which is not long after “dry powder”!).
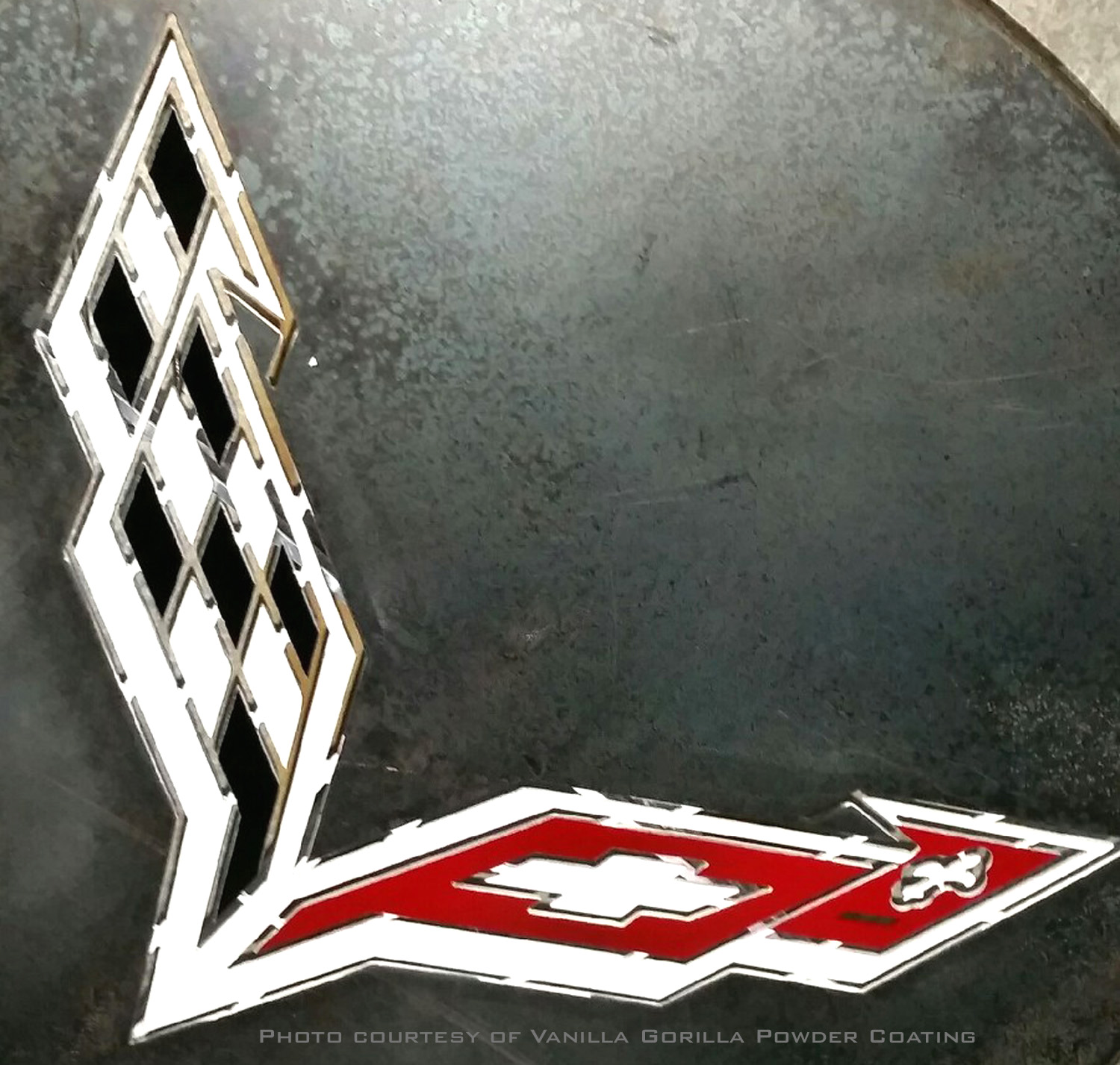
Table is Ready for last coat of silver-vein grey; Corvette symbol must be completely masked to achieve this.
The challenge is that when the powder is wet, removing tape will cause the powder to be “stringy” like melted cheese pulled from a piece of pizza. If you’re late pulling the part from the oven at the “melted” stage, letting the part cool for a few moments can be the difference between stringy and a “clean” tape pull.
Again, Experience and Practice Matter!
Viadon encourage you to try two tone powder colors on various parts of differing masses and materials, and with different powders, in order to learn the techniques necessary for the variables involved with each. Then, importantly, write down your results for what works! That way you can go back and reference it in the future. And have a roll of green and orange polyester on hand, at minimum, to work through the process with some lower cost tapes, or have a roll of glass cloth and/or polyimide for larger, more massive parts that require longer cure times.
Viadon has all the high heat masking tapes you need to successfully powder coat multiple colors:
A Few Last Points
- Removing tape from a warm part is almost always easier than removing it from a cold part. This can also reduce the incidence of powder flaking off from parts.
- To get the best lines between colors, if possible, remove all tape between colors before full cure. This softens the edge between the two colors.
- Alternatively, shoot the entire part with clear coat after partial-cure of first two colors, to reduce harder edges along lines.
- While 180°F to 200°F is typical for most powders as the right temperature to remove tape, some coaters remove tape as low as 130°F.
- First coat will increase resistance; adjust gun settings to compensate for this (lower voltage or limit current). Increase gun to part distance slightly – this slows powder delivery slightly and decreases current slightly. Due to these changes, powder delivery settings should be increased 10-20 percent.
Following these guidelines will help small custom powdercoaters have the best chance of success at powder coating parts with more than one color.
Experiment, practice, and write down results for various parts, tapes and powders to find what works best for you, so you can repeat successful results in the future.
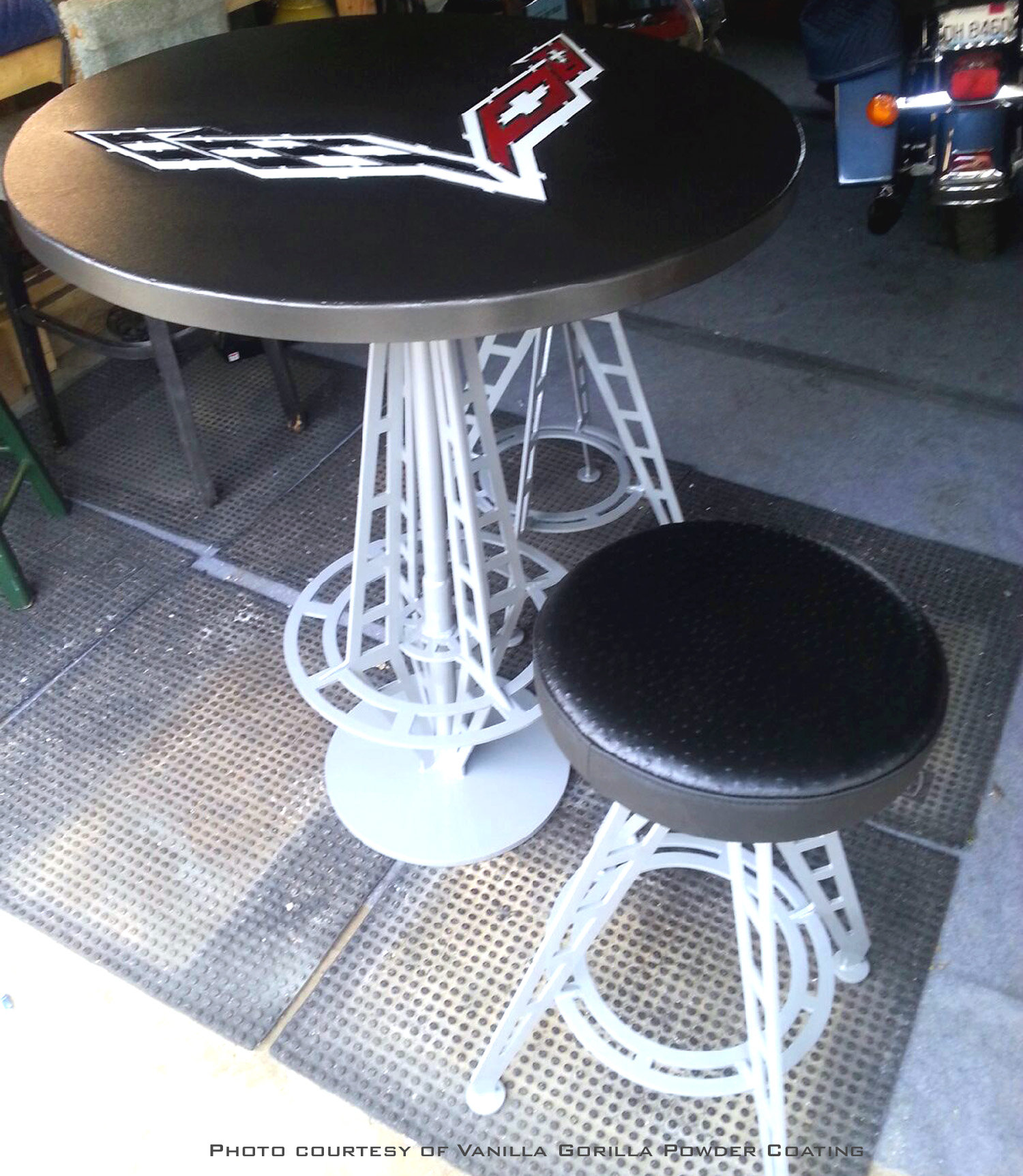
Multiple-Colors Powder Coated Table with Matching Chairs
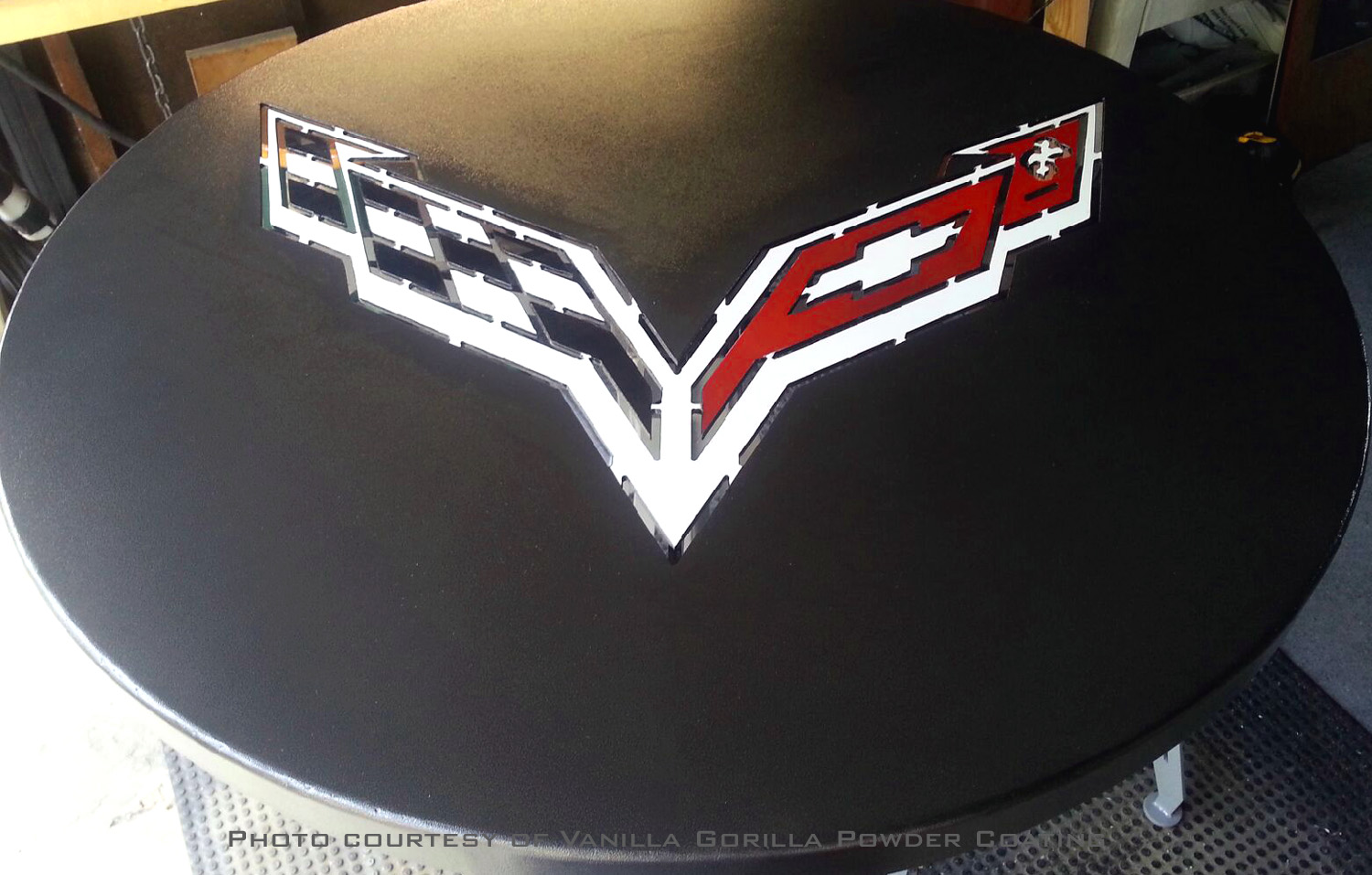
Completed Table and Chair Using Multiple-Color Powder Coating Techniques
Page updated May 24, 2021