Winter 2025
Winning at custom tape widths
With Viadon, you are not charged extra for custom widths of tape.
That's right, we slit most any width of tape and it's almost always a multiple of the basic 1" width price.
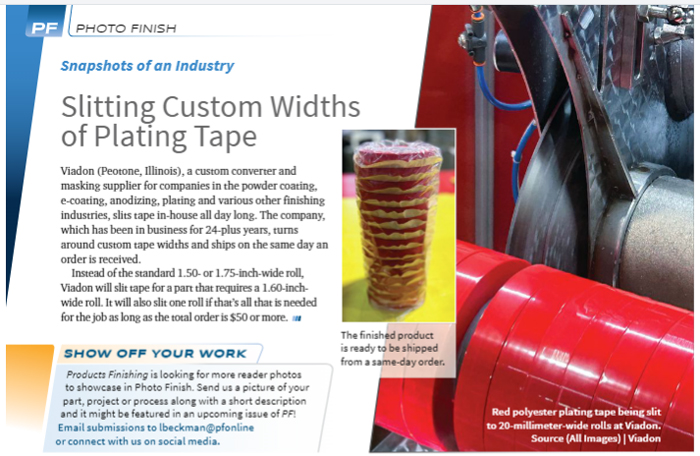
Want more details? Have questions? Give us a call or email. We answer our phone FAST and actually response to emails right away too - it's a few reasons why Viadon is, "A Cut Above" in the masking industry.
Summer 2024
Great customer service never goes out of style
Here at Viadon, we have this not-so-radical idea on how to stand out relative to other companies.
We do customer service better.
“How, exactly?” That’s a valid question, as what is perceived to be customer service can vary quite a bit.
First, here are a few things that irritate us, and what we feel should not be done as a consequence of that annoyance:
- Endless phone prompts, that starts out with “Our menu options have recently changed.” We are not a fan of having our time wasted, and so we think that’s not a great way to do things for our customers either
- Receiving emails without any way for us to respond. For example, having a note on it that says, “The inbox for this email address is not monitored.” Two things: Our Monthly Special emails have an “unsubscribe” option as well as our “info” email as a response option, and two, we do not send out emails from unmonitored addresses.
- A “Contact Us” form on websites that NO ONE ever responds to, because as one office actually said, “We never check those emails – we aren’t even sure how to do that.” Huh? How is that good customer service? Just take the form down already.
Granted, Viadon is a small company, so we have a lot flatter structure. As such, speed is easier for us. But it seems – and feel free to disagree – that responding to basic inquiries or having a real person answer the phone is seen as a benefit by customers.
What do we do differently?
ANSWER PHONE CALLS
For one, we answer our phones. Yes, we not only still have landline phones, we answer on the first or second ring during business hours – and by a real live person. We also do not outsource any customer service to somewhere that makes for language or communication problems.
PROMPT EMAIL RESPONSES
Secondly, we respond to emails, promptly. Good news, bad news, whatever – we work hard to make sure it gets a response right away. The flip side is we have had to follow up sometimes three, four or five times with a VENDOR to find out if they are shipping products we ordered from them – that is to say, the people to whom we give money. When we get crickets for days on end… that’s not good! It’s frustrating to us, and we have no good response for our customers when there’s no response from the vendor. It’s why we like partnering with companies that respond more quickly.
BEING SMART ABOUT ‘CONTACT US’ METHODS
Thirdly, while we do not have a “Contact Us” form, we do have a general inquiries email address. Either way, we think an ASAP response is the right move. Few things are as frustrating as sending an inquiry via a Contact Us form or a general inquiries email and getting… nothing.
INSTITUTIONAL KNOWLEDGE
Viadon has been fortunate in that we have five core employees, the most recent of which has been with Viadon since 2003. So our history of knowing our customers goes a long way towards creating an institutional knowledge base. That said, we are human. For example, someone up front may forget something, while another person in the warehouse might say, “This company never ordered that before.” It’s a means of self-correcting mistakes BEFORE they happen.
And just how well are we executing on all the above? Here is what a few customers have shared – unsolicited! – with us over just the past year:
“You all are the nicest, most efficient and the easiest company to work with! I recommend you to anyone who asks!”
“It's difficult for me to admit but I wish my firm had mastered responses to customers half as well as Viadon does.”
“You all are amazing. I appreciate the fantastic service.”
“Wow! You guys make me want to order something! I completely admire your customer service. I’ve never seen any company that was so attentive to the customer.“
Oh, one more thing: Be nice when responding - even when it seems a customer has asked a silly or redundant question. One that we recall was a customer that would contact us asking for how to convert fractional inches to the lowest common denominator fraction (i.e. – “What is 8/16?” Us: “That’s ½ inch.”) They weren’t stupid – they just needed help in an area we are better equipped to assist.
And metrics-wise, how’s this working out for us? We have grown since 2000. Okay, we were a little slow in the Great Recession – wasn’t everyone? – but since 2010 we have been on an upward track and never looked back. It’s not “explosive” growth – but sustained, controlled growth – which! – means we can service our customers optimally without getting overwhelmed.
Maybe a few of these ideas are things other companies can implement too. After all, while it seems “old school” and a lot of the new/fancy AI stuff is all the rage, maybe it’s just a simple lesson that some things – like great customer service - never go out of style.
Summer 2023
Powder coating tape tip: Masking large, open areas
Inflation has certainly done its share to make everything more expensive. What is even more expensive is having to re-coat a part because masking failed - due to said masking being tasked with something it wasn’t really meant to do.
For high temperature masking tapes, that may mean the use of a more expensive tape – but it will do the job right the first time, too. Ultimately, that saves you time, money, and headaches – because it lowers or eliminates the need for costly rework. Just be sure to charge accordingly.
What do we mean by all this?
When a large area needs to be masked off (anything 6” to 8” square or bigger, for example), it can be tempting to think that a large piece of masking tape is the best way to mask it. For large quantities, that’s probably true. For small quantities or one-off’s, consider this:
Tape the edges with 1” to 2” tape, while covering the center with paper (that has a flash point is 451F) or aluminum foil (check the cost per square inch/foot first).
But that’s assuming the area is all one flat surface. And that adds a wrinkle to this.
When the area is flat all the way across, the tape heats up at the same rate as the part does, so reaching the part mean temperature (PMT) for powder curing takes longer for the tape – just like the metal part. This is because the tape is literally touching, because it is adhered to, the part.
But what about something like a valve cover? There’s a narrow, flat surface area around the outside edges, but a larger open area that is covered with tape that is unsupported. In that section, the tape doesn’t touch any metal – just air from both sides. Doing the paper/aluminum foil trick with tape around the edge is impractical now.
Then what? Green or blue poly all the way around?
That might seem to save money, but the unsupported polyester in the open area heats up quickly, and over time, can shrink – and that can cause stringy, partially cured powder to get dragged across the flat surface of the valve cover. That leaves a bit of a mess, and additional time and work. What to do?
Try using a higher temperature rated tape across a large, unsupported surface that will heat up faster than the part. Viadon carries 425F orange polyester tape, and 500F polyimide (amber) and glass cloth (white) tapes that are perfect for these situations.
Other powder coaters do this routinely, because in the long run, they save time – and money – as a result.
Spring, 2023
Soaring inflation has touched us all, from eggs to electricity - it seems everything has gone up in price. But what adds insult to that injury is when companies tack on extra “fees” on top of already high prices.
Shipping? Add a fee beyond costs.
Handling? Add a fee for someone touching a box.
Used an online system to place your order without any human intervention whatsoever? Add a fee.
What is that about? It is ridiculous, isn’t it?
Well, Viadon doesn’t do any of that.
While we have had to adjust our pricing to account for our suppliers passing along higher costs to us, we have never added extra fees – flat or percentages – on TOP of already unavoidable higher prices. That’s just wrong, in our view.
So not only are we upfront about pricing and do not add random fees, we also ship most in stock items same-day when ordered prior to 12pm Central Time – and sometimes even when ordered later than that! We do our best to get your order out the door given that we slit all tapes to width at time of order. Plus, we always try to respond promptly and provide quotes quickly. How quickly?
A recent prospect shared this with us:
I want you to know how much I appreciate your response. I’ve sent countless inquiries on these and you are the ONLY one so far to respond!!! THANK YOU!
Total time from inquiry receipt to response sent on the above? 16 minutes. And other companies did not even respond to them? We cannot even imagine NOT responding – even if we have to no-quote because it is a job we are unable to do.
Want better service without the added fees AND fast shipping of mostly American-made tapes from a company that answers phones calls with a LIVE person during business hours?
Give Viadon a call today. It’s why we are, “A cut above.”
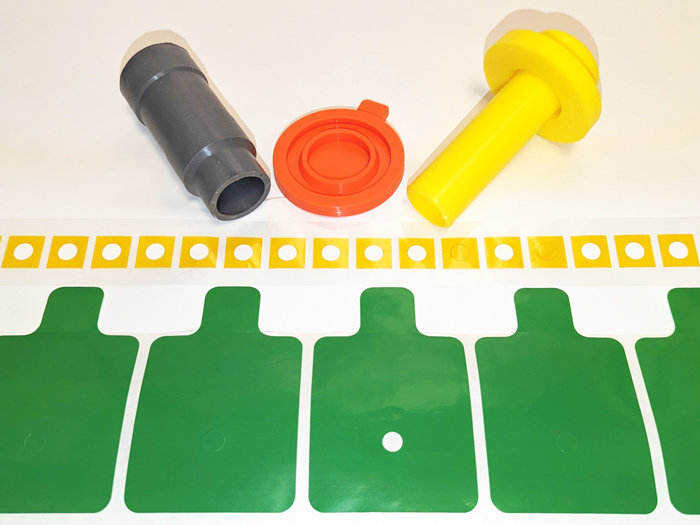
Autumn, 2022
Getting product TO our door
“Supply Chain Problems” has been one of the most challenging aspects facing nearly every industry over the past year or two. Viadon has worked hard to stay ahead of these issues – and largely has - by stocking up on tapes, caps and plugs as much as possible. But even with that foresight, one tape has proven to be short on supply for longer than anticipated: Our VHTC1 high temperature crepe tape (PG-21), with a max temperature of 325F.
For years, our VHTC1 tape has been the go-to masking tape for the finishing industry, particularly for wet-spray painters. Paper mills have been closing at alarming rates around the world, making the raw materials for paper-based tapes scarce.
An alternative became a necessity, as the situation is unlikely to improve in the foreseeable future.
Viadon searched high and low for comparable masking tapes to provide a satisfactory alternative that was also competitively priced. Many tapes exist that offer similar high temperature performance, but most of them have been substantially more expensive than our VHTC1 by 2x and sometimes 3x the price… until now.
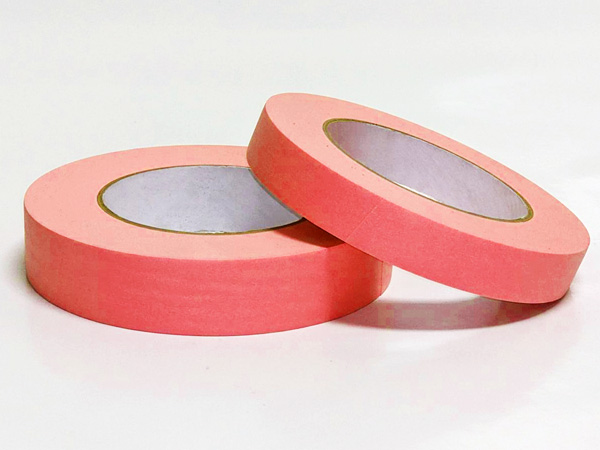
Viadon’s pink P325 crepe tape is a suitable, high-performance alternative in the high temperature crepe tape category. While the price is slightly higher than our VHTC1 tape, one thing it has going for it is imperative: Better availability! And the performance feedback we have received so far from customers has been that it works in nearly all the same masking tape applications. With the pink color, it also provides better visibility for removal.
Want to try a roll or two? Give us a call for current pricing. If enough customers continue preferring it, we will add it to our product pages as a stock tape.
Another reason why Viadon is A Cut Above.
Summer, 2022
All time highs... and not the summer heat
It has been quite the year and a half since Covid-19 changed things! Price fluctuations, supply chain disruptions, shipping issues, pandemic-related challenges. Can we all just get a break already?
And yet, through it all, Viadon has thrived – our total sales have continued going up. Our customers have been incredibly loyal – and we appreciate all the new ones too. We are incredibly grateful to the purchasers, small shop owners and everyone else in between with whom we interface for placing their trust in us repeatedly, despite the occasional bumps in the road.
It is those valued customers and our trusted vendors who have helped Viadon continue to grow and provide the very best products at competitive prices – all while doing it with mostly American-made tapes and silicone sheeting products. Why? We believe the USA-manufactured products are consistently better – and we provide them at prices that rival and even out-compete those imported ones.
Perhaps this is why - after nearly two decades of ISO certification - Viadon continues to receive a 99% satisfaction rating from our valued customers in ISO surveys. Is further improvement possible? There’s not much room to get better, but we will keep trying! Why? Because we value our customers and want to keep providing the fast and friendly service they have come to depend on since September 2000.
It's why Viadon is ‘A Cut Above.’
Winter, 2021
When the shipping hits the fan
You may have noticed items missing from store shelves, seen delays and backorders from suppliers and experienced unanticipated – and sometimes quite significant – price increases.
Viadon has not been immune from this. Our logistics partner shares that most of these circumstances, in one way or another, can be traced back to Covid-related issues. Whether it is insufficient workers (due to sickness) to produce items or get them shipped/delivered, spikes in demand causing supply shortages and/or shipping bottlenecks due to those surges of buying, nearly all of them have that same cause in common.
During this time, Viadon has been working diligently to maintain our stock products and get custom parts made and shipped quickly.
- For one, stocking mostly American-made tapes has helped us maintain an almost-always available supply of tape and die cuts.
- And back at the beginning of the year, Viadon was already buying additional caps and plugs to maintain sufficient stocks of those parts.
- To date, we have been able to acquire new tooling for custom die cuts with only a slightly longer lead times.
- One significant challenge right now is custom molded parts. Very often customers choose to air these parts in from our overseas molding partner. At present, the holiday season is upon us and currently there are 60+ container ships waiting to dock in LA / Long Beach, in addition to currently-unloading ships.
As such, many importing industries with the option to do so are choosing to bring in product via airfreight just to get it stateside before Christmas (even at increased cost). Unsurprisingly, we have seen some delays due to this, though so far they have been minor. Our logistics partner anticipates this should begin to ease sometime in 2022.
This is all to say we have been working hard and will continue to do our best to try and provide you with the materials you need so you can finish things right. We do ask that in the event an item is out of stock or somewhat delayed, please be patient and know that we are doing all we can to acquire the missing item. And as best we can, we will keep you updated on the progress of those products.
This is a challenging time for everyone, but Viadon continues to rise to that challenge because we continue to believe we are, A Cut Above.
Thank you for your business. Know that we will keep working diligently to earn it every day.