Your guide for powder coating masking advice
TO GO DIRECTLY TO LINKS FOR PLUGS AND CAPS, SCROLL DOWN TO WHERE PHOTOS START.
This guide is so you can better understand tapes, caps and plugs options to achieve the best powder coating masking at the lowest cost that is fast to apply and easy to remove. We have included most standard as well as some non-traditional masking ideas to help you learn some new methods for masking tricky or complex parts for powder coating.
But first - proper prep is an imperative.
Surface Preparation
This is one of the most important aspects of masking for powder coating, especially for tapes. If you do not clean parts fully, the tape will not adhere well (and your powder may not stay on either!). This is why all of our tapes pages for masking recommend starting with a clean, dry part before applying tape.
Always perform a thorough cleaning of the part, using an appropriate cleaning agent (for example, a detergent in water, a steam cleaner, wipe with acetone, etc.) for the type of metal having oils, greases or other dirt, dust or detritus removed from it. For some custom or aftermarket work, it may require the removal of the existing coating or plating prior to cleaning.
After these steps are complete, avoid touching parts with bare fingers – use gloves so no oils or other contaminants from your hands. Depending on the part, there may be additional steps needed, such as:
- Chemical pretreatment (such as iron phosphate for steel parts – this provides a barrier against oxidation)
- Blasting of part (for removal of loose metal and/or a better surface profile)
- Oven bake for outgassing (a secondary wash or blast may be necessary)
Every part is different, so this page does not cover every scenario, but many similar types of parts require the same steps or processes. Other powder coaters are often helpful in this regard, but powder suppliers and especially chemical pretreatment companies are the best resources for providing you good guidance for a specific part you may be working on.
Masking options overview
The part is clean and prepped for masking. Now what do you use to keep certain areas free from powder coated? That depends on what your customer needs masked on the part – here is a quick overview of available masking, from plugs and caps to tape options.
- Tapes - for both slit rolls and tape die cuts, powder coating masking tapes are genearlly limited to materials that can withstand 400F (or more) for 30 to 60 minutes. This usually means only tapes with a silicone-based adhesive, applied to a carrier that can also withstand such heat requirements, often polyester, fiberglass cloth or polyimide (Kapton type film).
- Caps and plugs - While there are a few materials that withstand 400F or more, cured silicone rubber is the least expensive and most-often used material. It remains flexible after repeated cure cycles, powder is often readily removed from the surface, and it is the most cost-effective high temperature rubber for plugs and caps.
Masking holes during powder coating
Seems simple, right? “This hole must remain free of coating.” While some masking needs are simple, many are not so straightforward - some may require a first thread to also be masked. Others may need a flange area uncoated around a hole. There are a lot of ways to plug a hole! Therefore, a wide range of plugs exists, from regular tapered plugs to specialized plugs that can mask through holes and first threads of chamfered areas and have handles for easy application and removal.
Here is a short overview for each of the more popular industrial masking options useful in a wide range of holes that require plugs for powder coating:
For blind holes, consider these plugs:
Tapered plugs – good overall powder coating masking plug - the most popular and most-used for powder coating.
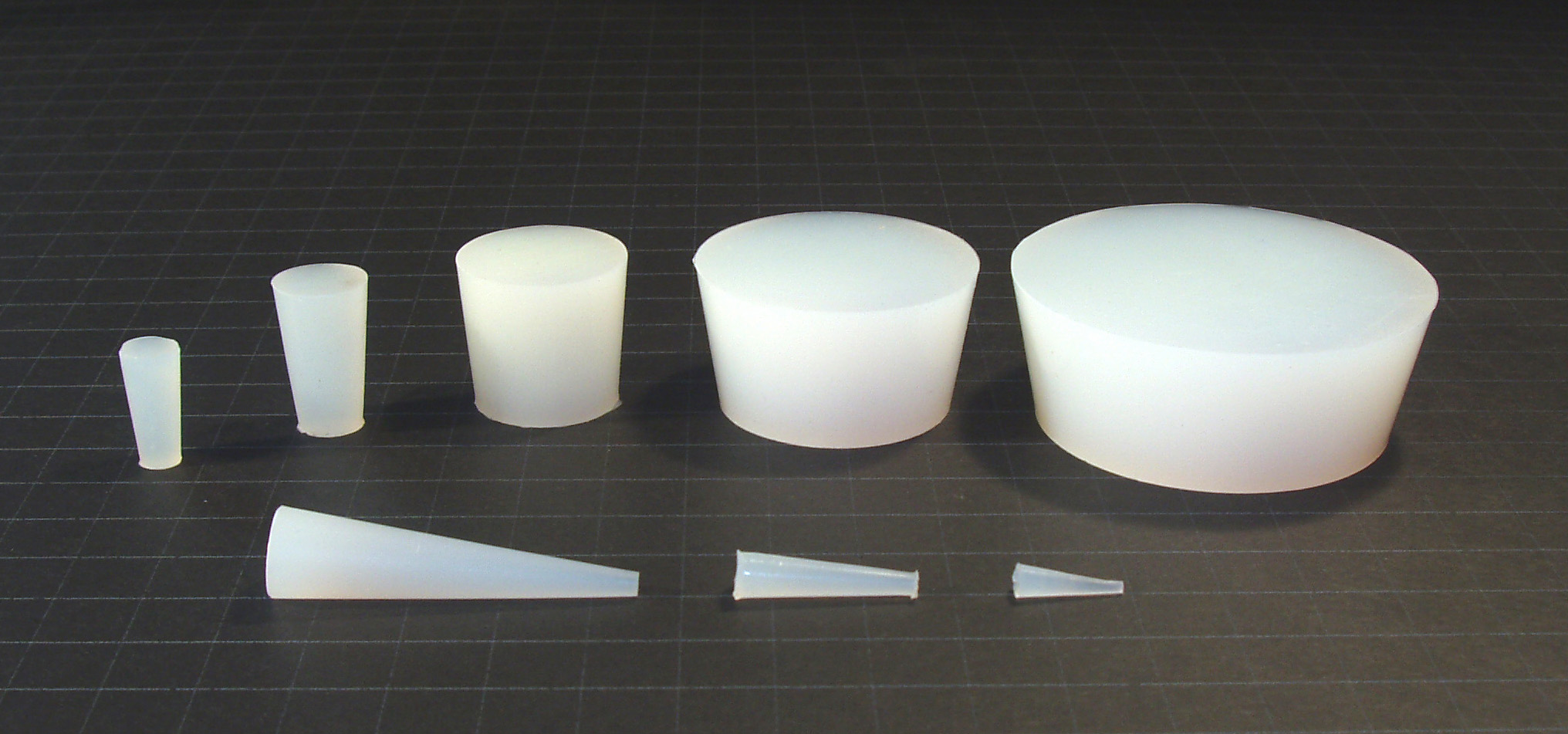
Tapered plugs with handle – same as above but insertion / removal in deep holes is easier and faster. Also makes it easier to "twist" the plugs into place.
First thread masks – masks top thread and internal threads for blind holes, which eliminates the need to chase threads with a tap after coating.
Flangeless plugs with ribs/handle – work well in threaded holes, deeply-seated holes, or when an extra “twist” is necessary to ensure a plug is well-seated in a hole. Have somewhat less of a taper, and occasionally work in shorter through holes as well.
Tapered flange plugs – tapered with hollow interior and has a flange at the wider end. Typically inserted into a hole with the flange masking a concentric area around the hole, usually for grounding.
Multi-flange plugs – a unique design that allows a single plug to be used in multiple hole diameters. Also useful for masking first-threads or chamfer lead-in surfaces of smaller threaded holes.
Hollow tapered plugs – larger silicone plugs get expensive quickly due to the amount of silicone used. The hollowed out, narrow end of these plugs reduces cost. In addition, you can insert this type of plug into larger holes to achieve greater friction – better keeping the plug in place and often avoiding blowouts from trapped, heated air.
For through holes, consider these plugs: 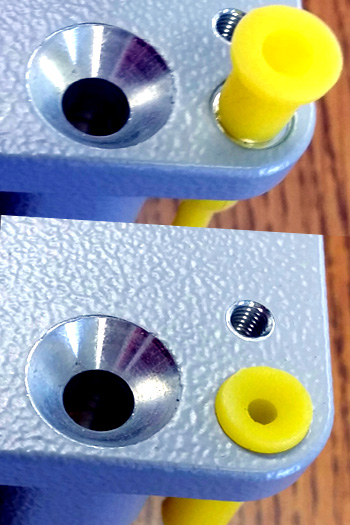
Pull plugs – the go-to standard for through-holes, has both a “tail” handle to insert the plug, and wider plug section that gets "pulled" into place to mask the hole.
Flanged pull plugs – ideal for threaded through holes when the first thread must be free of powder as well to avoid retapping. To remove, just pull the plug out the same direction it was inserted; the flange "folds" as the plug is pulled through the hole.
For blind or through holes, consider caps:
Silicone caps – yes, you can use caps to mask holes! Do not overlook them as a powder coating plug option. The straight-sided wall can be quite useful for longer, straight-sided through holes up to 2” in diameter. These masks can be “nosed in” (pushed in curved end first) to a through hole using a dowel or other push rod. Best for non-threaded holes but caps have a wide range of masking uses in this manner. Look at the caps OD (outside diameter) compared to the hole that needs a plug – aim for a cap that is 0.015” to 0.030” larger than the hole diameter.
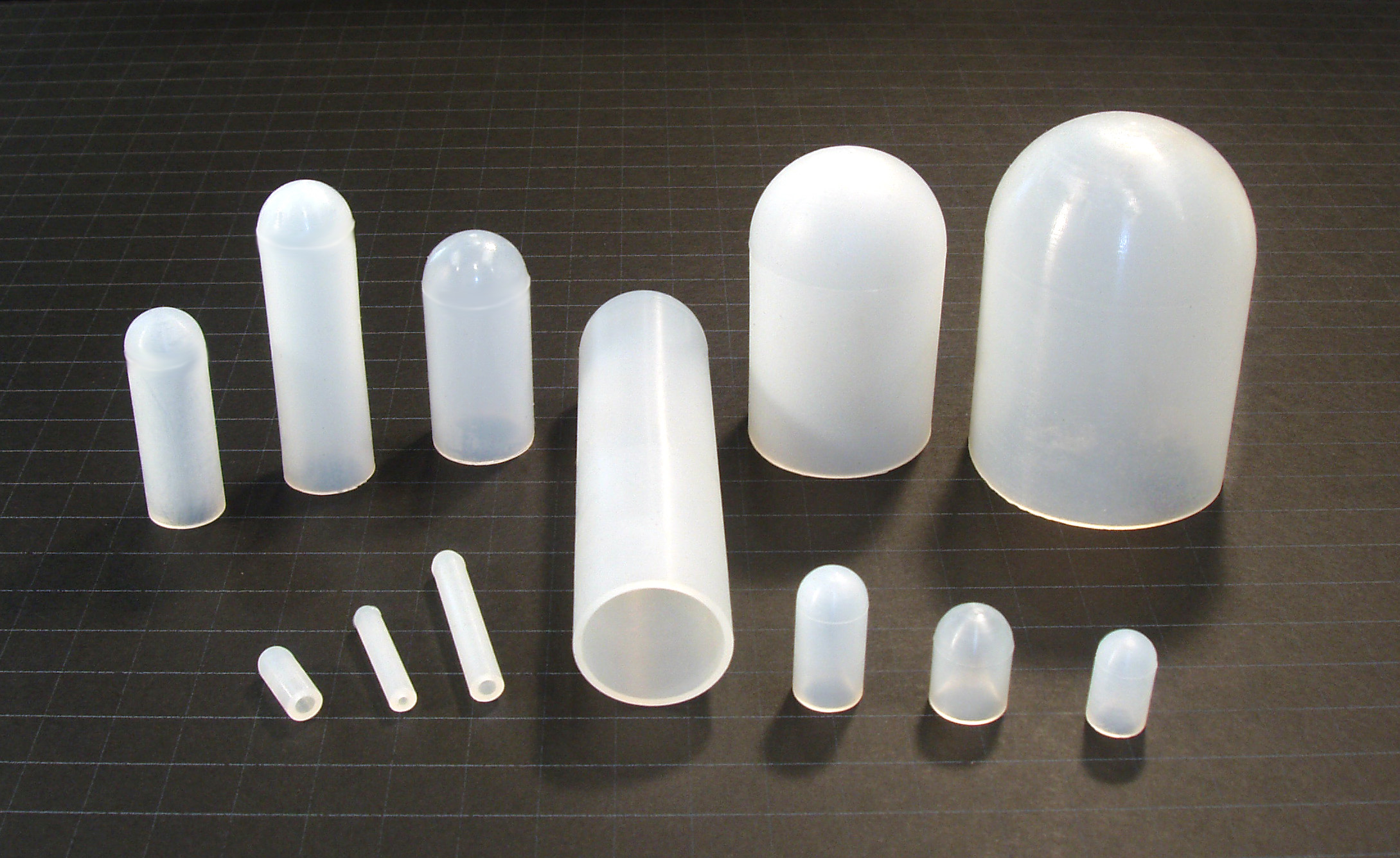
Flange caps – same as above, but provide a concentric, perfectly centered masked area around the hole that will also be masked – ideal for grounding surfaces, etc. Just insert the cap "nose in" to use it as a plug.
Masking tubes, threads or studs during powder coating
While caps are a bit more limited in the types available, there are some interesting options worth considering that you may not have realized exist:
Straight walled masking caps – the standard for masking short threaded parts. In general, one diameter of this kind of cap masks a single diameter of stud or bolt, perhaps two at most. But if you mask a lot of the same size, this is a great option to use. Various lengths are available for some more popular thread sizes assist with reducing trapped air so the caps do not creep up on parts as heated air expands underneath (which can cause stringy powder defects) or blow off in the oven. Need a custom size cap or more elaborate design? We can do that – email or call for more information.
Expandable caps – a useful multi-size type of cap that has a ribbed interior at the open end, and a wider cavity above it up to the top. Ideal for masking a wide range of thread sizes while only needing to invest in a small collection of caps. Great for job shop custom powder coaters who never know what size threaded or non-threaded parts they must mask off. Watch for trapped air though. A simple slit at the top can help release heated air – use a knife or scissors to quickly make such a cut.
Flange caps – cap a threaded or non-threaded stud and simultaneously create a perfectly centered grounding area around it.
Tapered flange plugs – while these are tapered on the inside, they have found use as a cap at times.
Tubing – got a long stud or thread to mask, but stock caps are too short? Cut some tubing to mask that problematic part. Tubing can be cut long and left open or capped off with a regular cap that fits over the OD of the tube. When adding a cap like this, cut the tubing only ¼” longer than the metal to be masked to reduce trapped air that will get heated up.
High temperature tapes – Many powder coaters will wrap studs or threaded areas if they do not need a lot of caps on hand. While a bit more time consuming, it may be a cost-saving option if the quantity of studs/threads to mask is low.
Not seeing the masking cap or plug you need? Send us an email or give us a call. We are here to help you, and can search and obtain a wide range of other stock masking parts and design custom molded masking parts too.
Powder coating masking tapes
Tapes provide amazing flexibility for masking parts. When a plug or cap just will not cut it, tapes are often the answer. What should you use for powder coating masking tapes? The following is an overview of some popular options that exist so you can choose the best tape for your needs.
What kind of surface are you masking?
Masking flat surfaces for powder coating – some of the thicker tapes are good for masking off flat or large surface areas. Standard green polyester powder coating tape is perhaps the most-used of these options. If the area is much wider than about 4” to 6” though, consider using aluminum foil or paper to mask over the large interior section and taping around the outside edges. Note that paper’s flashpoint is 451F; be certain to only use it well below those temperatures. It can also get scorched and leave charred paper, so be cautious when using it.
Masking curved surfaces for powder coating – for complex curved metal, a thinner tape is often a better option. Blue polyester tape is made from a 1 mil thick PET material, and it follows complex curves better than thicker polyesters. But interestingly, high temperature glass cloth tape – a rather thick powder coating tape at 7 mils – is often used for wrapping complex areas due to how it will fold down upon itself better than thicker polyesters or polyimides do.
Temperature
Some powders require more heat to fully cure. Fortunately, most powder coating caps and plugs are made from silicone rubber that withstands up to 500F or more for repeated uses. But tapes are different when it comes to temperature rating, depending on how they are made. Nearly all high temperature powder coating tapes use a silicone-based adhesive system, as most rubber and acrylic adhesives will not withstand temperatures over 325F to 350F.
An often-overlooked aspect of these tapes is that they all have pressure sensitive adhesives (or PSA’s). In order to achieve good adhesion to a part, that means some pressure must be applied to the tape to activate the adhesive so it will adhere well. Moderate finger-pressure is often sufficient, but for wide surfaces, a small squeegee or roller may be useful.
These silicone adhesives are applied to different backings, also known as carriers (since they “carry” the adhesive). Here is a short overview to help you choose the best one for you:
Polyester tapes: Good for most powder coating masking up to 400F or even 425F. Green polyester tape is the most used tape for masking powder coating. Blue polyester is thinner and is better for masking curved surfaces. Our orange polyester tape withstands 425F and is often used for two-color powder coating or for masking large open areas (the open side of valve covers, for example) as the tape not touching the metal heats up faster than tape adhered to the part so it resists shrinking better than other options. Lowest cost, but also lowest temperature.
Polyimide tapes: Best for when oven cure exceeds 425F and will even withstand up to 500F. Has a silicone adhesive, available in 1 mil, 2 mils and 5 mils options. Sometimes referred to with the DuPont trademark name of Kapton, but polyimide is usually the correct term as that is the generic name for this material. Polyimide tape with silicone adhesive excels in two color powder coating applications, or when larger/more massive parts must be kept in an oven longer to reach the necessary PMT (part mean temperature) for full powder cure.
Glass cloth tapes: Only limited to 500F by the silicone adhesive system, otherwise it could withstand higher temperatures. Considered a heavy-duty powder coating masking tape and is ideal for heavy powder applications of 7 mils to 10 mils (or more) as it is difficult to tear and will remove through thick powder layers. Often used for masking buss bar contact surfaces.
Tape application and use
Tape should only be applied to clean, dry parts. Trapped oils or other contaminants should be outgassed prior to masking. Most powder coating masking tapes are designed for intermittent use (typically means 60 minutes or less at maximum temperature rating) for a single cure cycle. Many powder coaters have found that by using higher temperature rated tapes such as polyimide or glass cloth, they can use these for longer oven cures at lower temperatures than the tape’s maximum or for two color powder coating jobs.
After coating is cured
Removing powder coating tape
Very often tape is best removed while the part is still warm. The adhesive is easier to peel off in scenarios like this. In some situations warm removal is not possible – in that case, remove the tape at a 90 degree angle from the part surface for best results.
Discard tape in accordance with any and all local or state regulations. Do not re-use; adhesive may bond to part or fail in other ways that are detrimental to clean tape removal and/or maintaining clean edges at powder/masking lines.
This should help get you acquainted with the basics of masking for powder coating. All of the products discussed above can be found on our website. If you have questions about uses, application, removal or need a custom masking solution, feel free to reach out to us via phone or email and we will do our best to assist.
Powder Coating Masking Advice
Got a challenging masking project? We're here to help! We have looked at thousands of different masking needs over the years for powder coating, and will always try to find you the least expensive way to mask parts quickly and effectively.
Sometimes that means off-the-shelf parts we have in stock, and other times that may mean an upfront tooling cost that saves you money down the road. Any way you look at it, we are here to help you solve your tough powder coating masking problems with proven powder coating masking techniques so you can better serve your customers.
Give is a call at 866-534-3900 or email us at [email protected].
Lists of the very best powder coating tapes, caps and plugs. We have powder coating masking advice here, too.